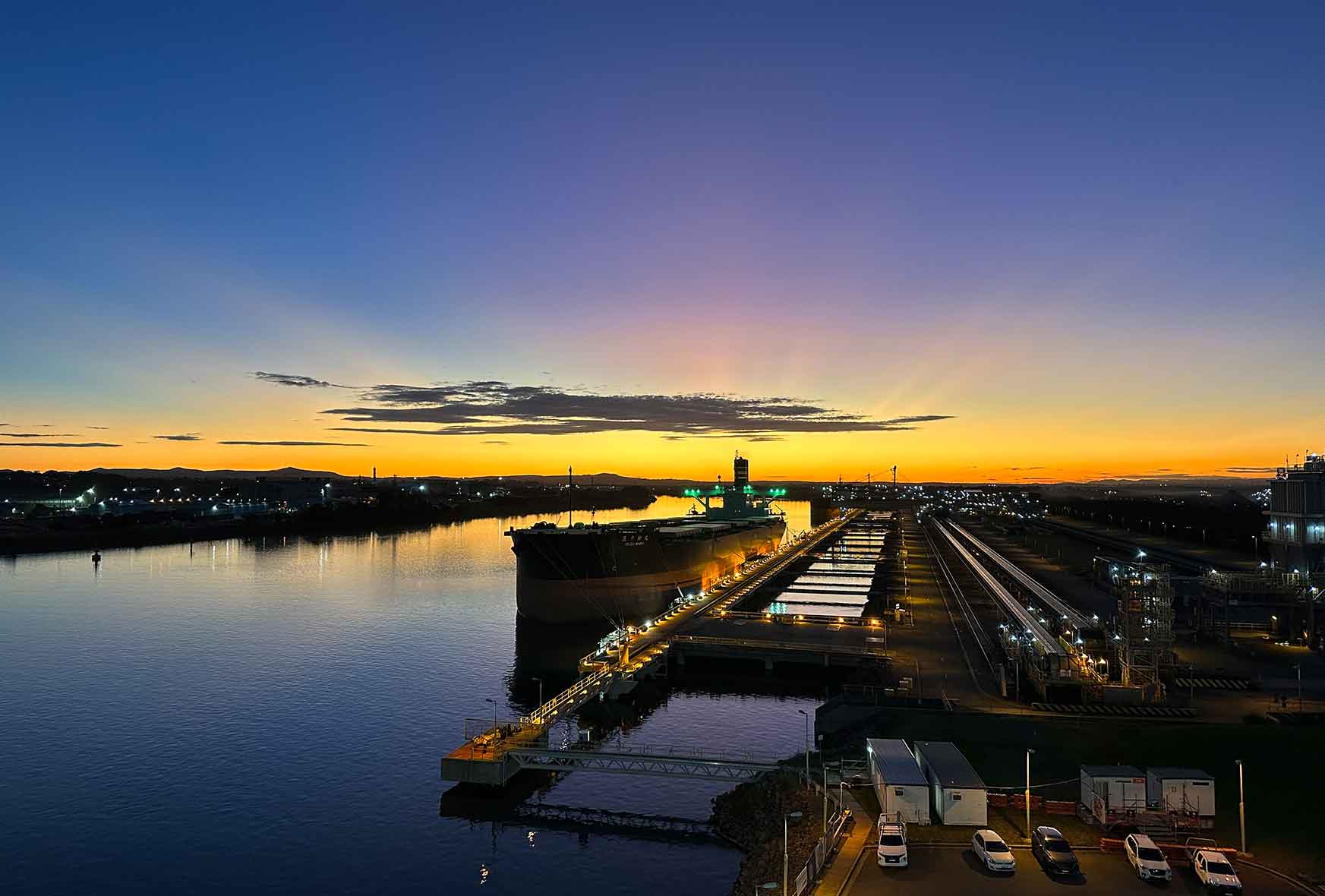
Seeking to improve port automation?
Detect and inhibit collisions. Improve visibility and efficiency.
Experience shiploader positional awareness and minimal errors in your process with Axo33 SHIPS™ Get 3D visualisation, collision avoidance and automation, maintain availability, find faults quickly and improve safety.
Your digital twin for shiploading success
Get complete visibility over your shiploader operations
With zero collision incidents in more than 100 months of active operations, Axo33 SHIPS™ is your number one choice for incident reduction.
De-man and de-risk your shiploader process with our complete port automation system with tools that assist loading, protect personnel and help eliminate accidents.
Harness digital twin technology for 3D visualisation to maintain availability, minimise incidents, find faults quickly, and sustain confidence in optimised performance. Detect movement and collision risk with 3D modelling, accurately determining position and movement regardless of vessel type, shape and size.
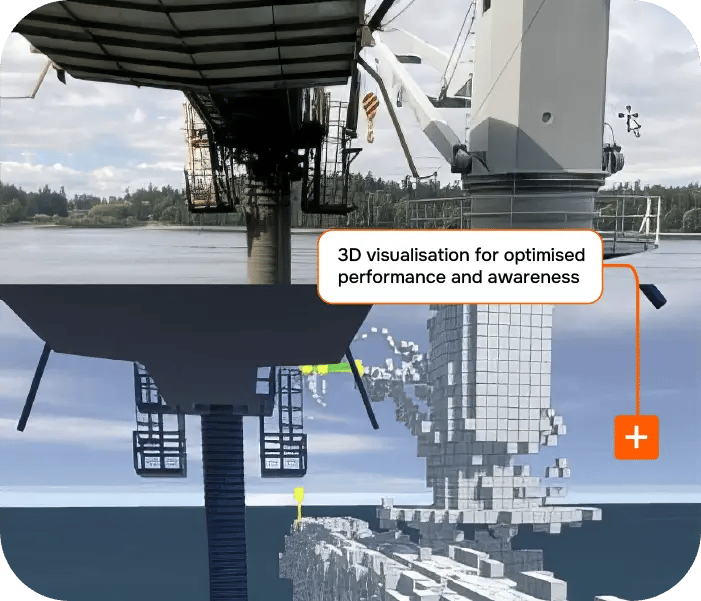
Your grey-box solution for greater inhouse control
Maintain control over your own systems
Minimise collisions with advanced anti-collision, measuring drift and draft and getting real-time detection alerts for load safety, correction, and suction force detection.
Enjoy the control of intelligent software that integrates with your own systems, enabling you to bypass ours if you want more manual control. Simulate offsite to de-risk tricky loads and minimise downtime. Bench test laser positions prior to commissioning for greater confidence. Eliminate blind spots and get adequate coverage, without impacting production.
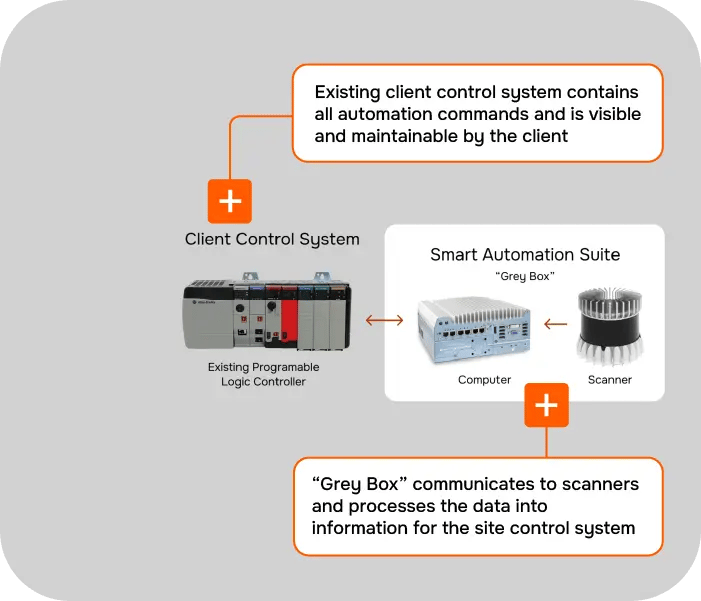
Large-scale improvement for minimum risk
Achieve enduring performance improvements
Continuous performance improvements come from systems you can trust. With Axo33 Smart Automation Products you keep control over ongoing costs by being able to inspect and maintain your own systems with ease. Enjoy minimal hardware investment and the confidence that our systems will never bring yours down.
Gain peace of mind, by working with technology partners with industry-proven software that does not require costly recalibration, and boasts a track record of successful implementations. Access certified integrators for improvements or additions to your system.
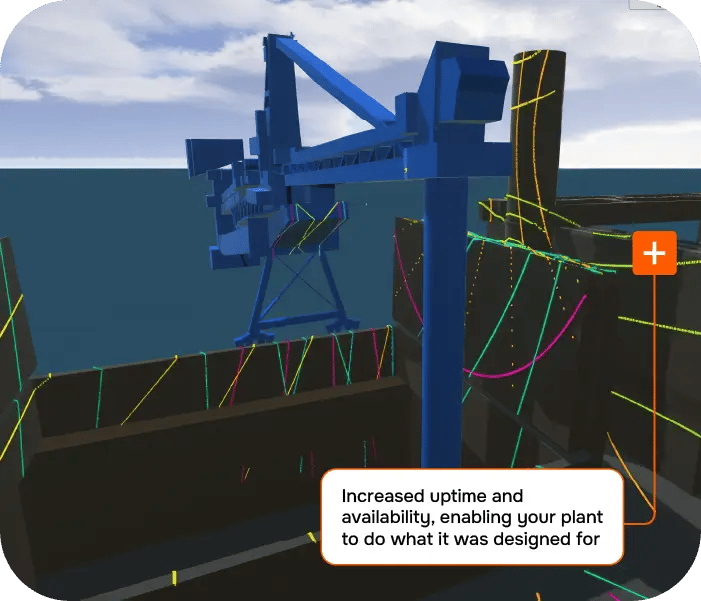
FAQs
How does Axo33 SHIPS™ detect and inhibit collisions?
The anti-collision system first builds an accurate 3D map of the vessel using millions of data points from low-cost, long-life LiDAR scanners that are suited to the harsh conditions of a shiploader. This establishes a real-time protection zone surrounding the ship loader’s boom and shuttle, its spout/spoon and the operator cabin. The improved visibility eliminates blind spots. Any object entering or nearing these dynamically defined zones will trigger a collision or inhibit unsafe movement. Key separation distances for the ship loader are available to the PLC for actioning including, alarm, slow down and inhibit. I.e. all control resides in the existing machine PLC.
How does vessel drift detection work on a shiploader?
Vessel drift detection monitors for unexpected vessel movement such as drift due to a broken or loose mooring line. Early warning enables the operator to respond in a safe and timely manner. With the addition of berth-mounted scanners, this detection can be performed anytime.
How can I ensure the shiploader is located at the correct hatch for loading?
Our hatch detection module is an operator support tool that uses advanced object identification to determine hatch state - open/closed, dimensions, edge identification and deck gear. This information can be used by the PLC to ensure the shiploader is at the correct hatch for loading.
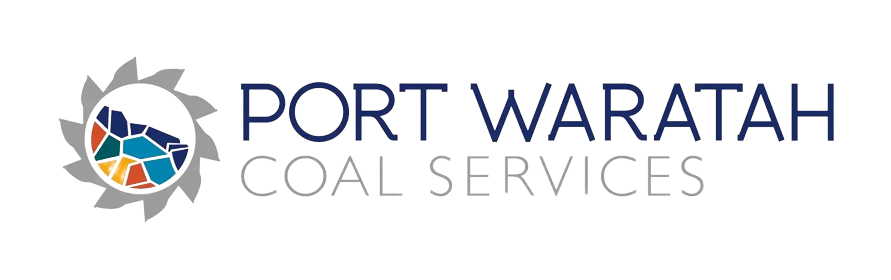
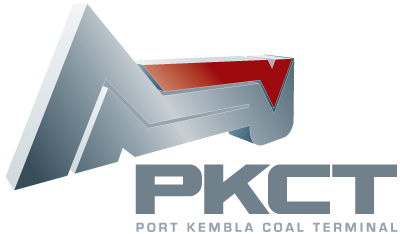
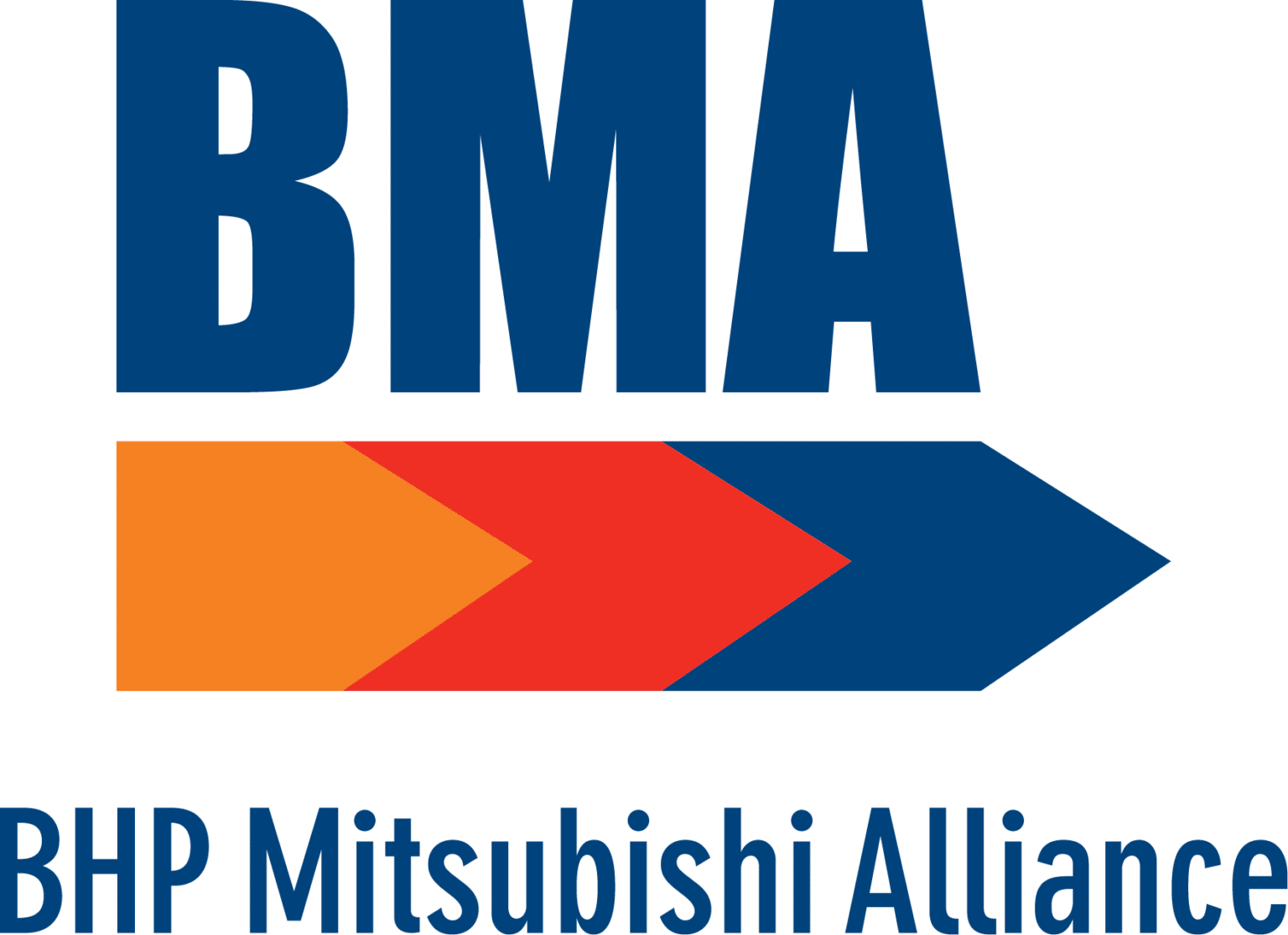

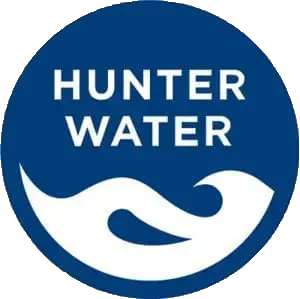
What our clients say
Geoff Irvine
Rockwell Automation
“We are delighted to have collaborated with MRA and this high value application.
The Smart Stockyard Management System is a key piece in bringing the “Connected Mine” to life for our mining customers.”
What our clients say
Anthony Manousso
Anglo American
“The coding that MRA developed within the ControlLogix PLC is extremely efficient and reliable. We are now using it for 98 percent of loading. This TLO system is an integral part of our pit to port operation.”
What our clients say
Travis Burton
Port Kembla
“The stockpile modelling and laser optimisation were major factors in our efficiency gains.”
Anti-Collision Systems in Canada’s Largest Port
The Port of Vancouver is the largest port in Canada and the fourth largest in North America by tonnes of cargo. The process of transporting bulk materials across the ocean often involves ship loaders depositing onto bulk carriers. A ship loader is a large machine on the port that uses a boom arm to dispense materials such as coal, iron ore, bauxite, and alumina onto the carriers.
Given the large size of the ship-loader there are many blind spots around the vessel which can lead to collisions that threaten personnel, damage valuable assets, and limit operations.
These collisions can be avoided, as they are often caused by the operator having low visibility.
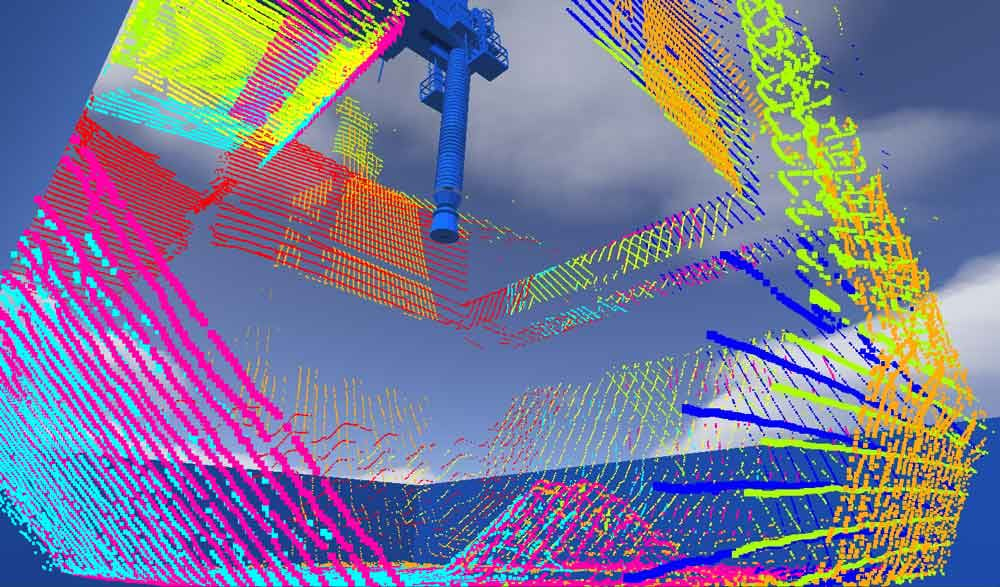