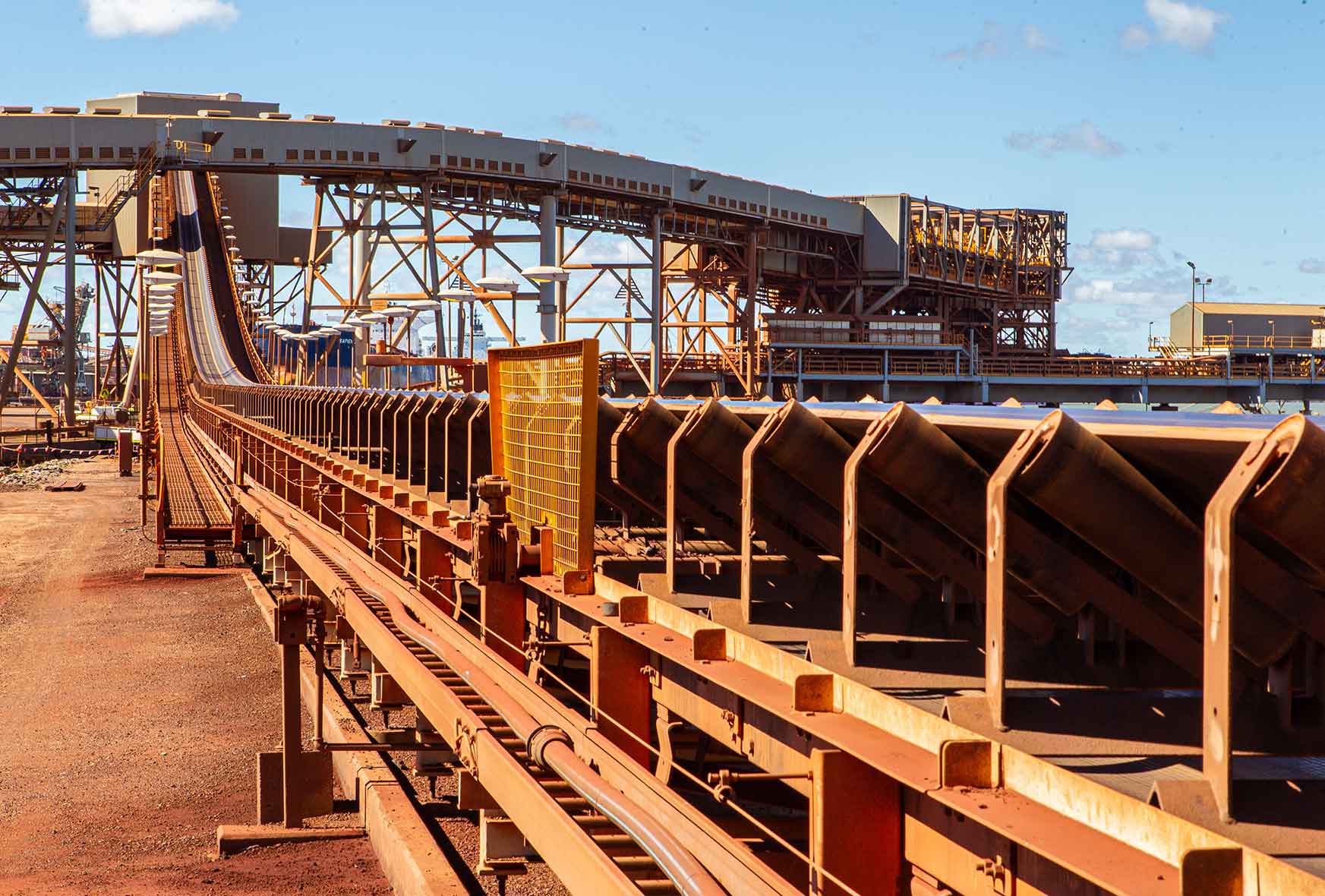
Overcome the most challenging of mining conveyor environments
Optimise conveyor start-up, speed ramp and load sharing
MRA’s conveyor optimisation model (COM) can help you overcome the most challenging of conveyor environments to ensure your overland conveyor systems operate smoothly and efficiently for minimal cost.
Whether facing challenges with distance, difficult topology or load variability, our COM is designed for the PLC control system, and works independently of the variable speed drive solution.
Uniquely, our solutions are assembled offsite in our simulation environment, to optimise dynamic control during mining conveyor start-up, speed ramp and load sharing. Our system is also designed to minimise over-tensioning and rope dislodgement.
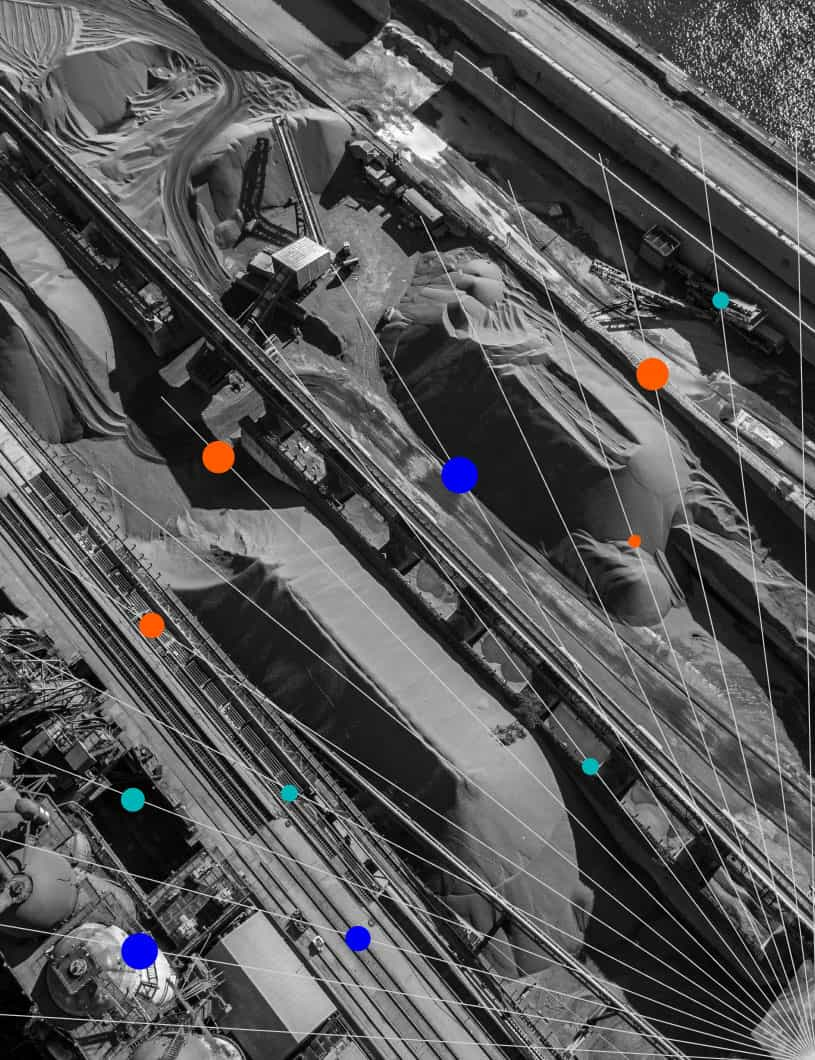
Benefits
Requires minimal downtime to install
Cost-effective to implement
Requires minimal onsite resources for commissioning
Improves conveyor life expectancy
Provides vendor flexibility as it is hardware agnostic to the variable speed drive for replacements
FAQs
What are the main types of mining conveyor systems deployed today?
There are three types of mining conveyor systems that are deployed on bulk materials handling sites:
- Overland conveyors: Designed for long-distance transport, connecting mines and ports efficiently over extended distances.
- Underground belt development and production conveyors: Feature multiple drives and dynamically changing lengths or configurations to adapt to the intricacies of underground environments.
- Multi-drive conveyor systems: Feature separated drives, such as motors pulling and pushing the conveyor. These systems demand precise coordination between drive stations to ensure optimal belt tensions during startup and operation.
Why is offsite simulation of mining conveyor systems advantageous?
By assembling our mining conveyor systems in a simulated environment, the time and resources required on-site to commission and tune the system are reduced. This ensures the system is fit for purpose, reduces downtime on operations, and limits stress on the mechanical components of the conveyor system, increasing life expectancy.
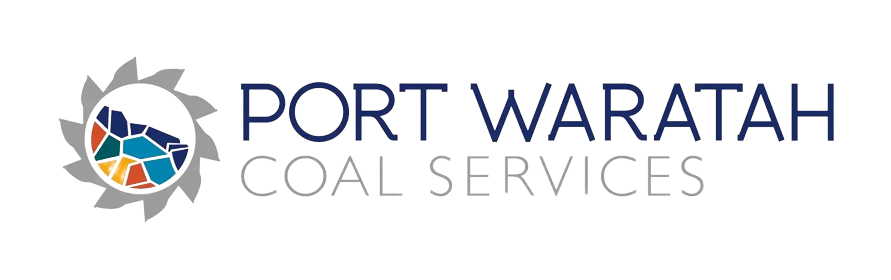
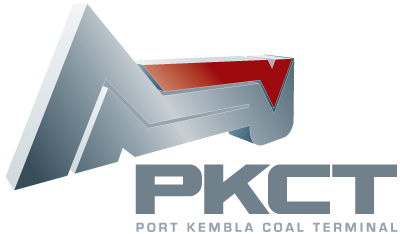
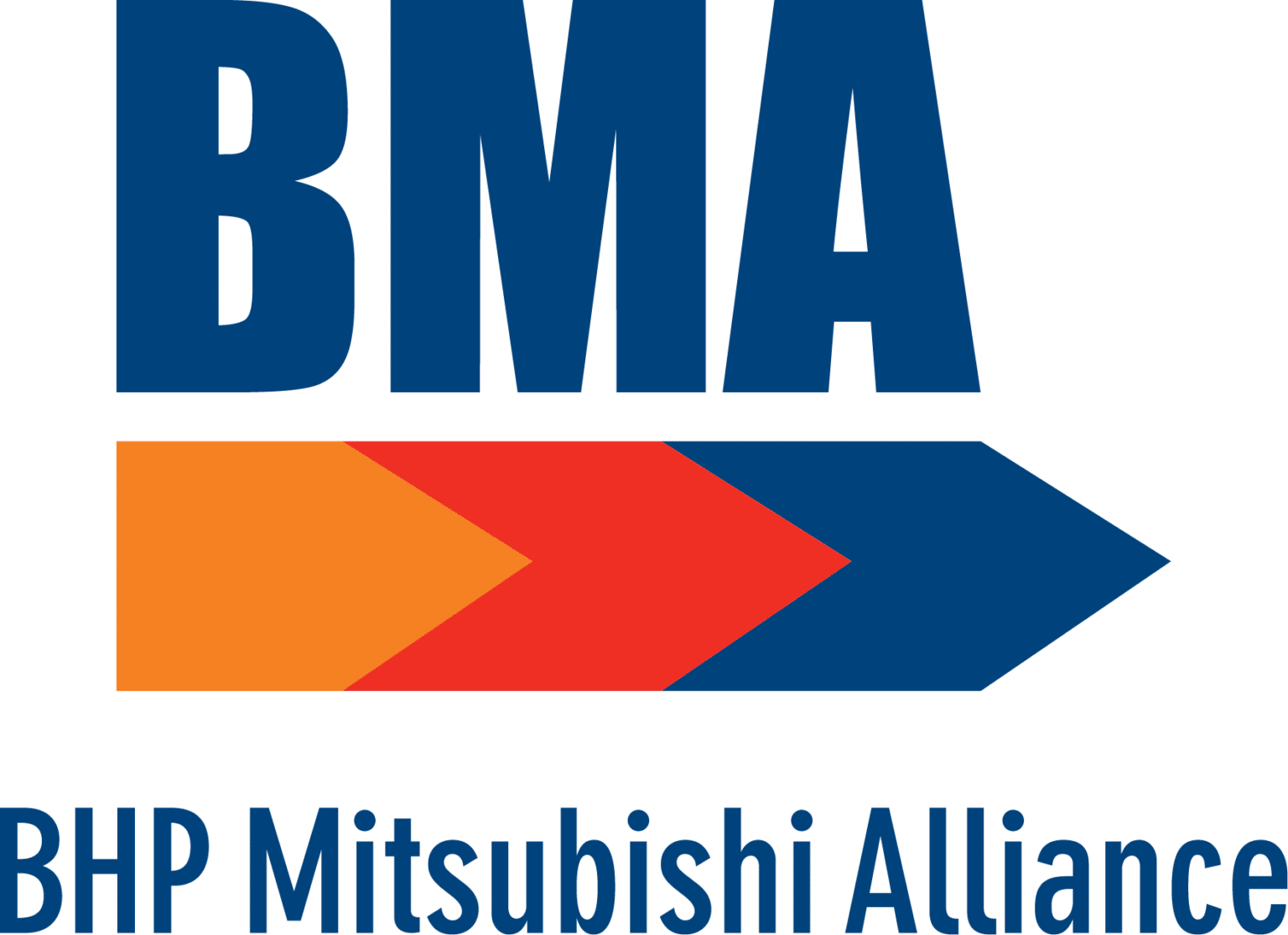

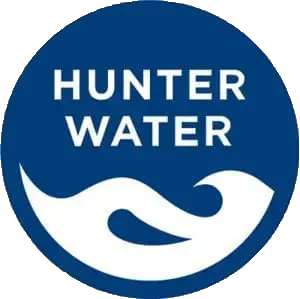
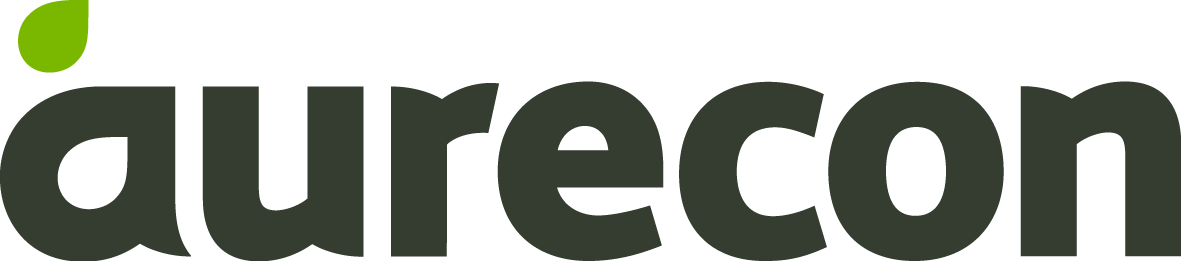
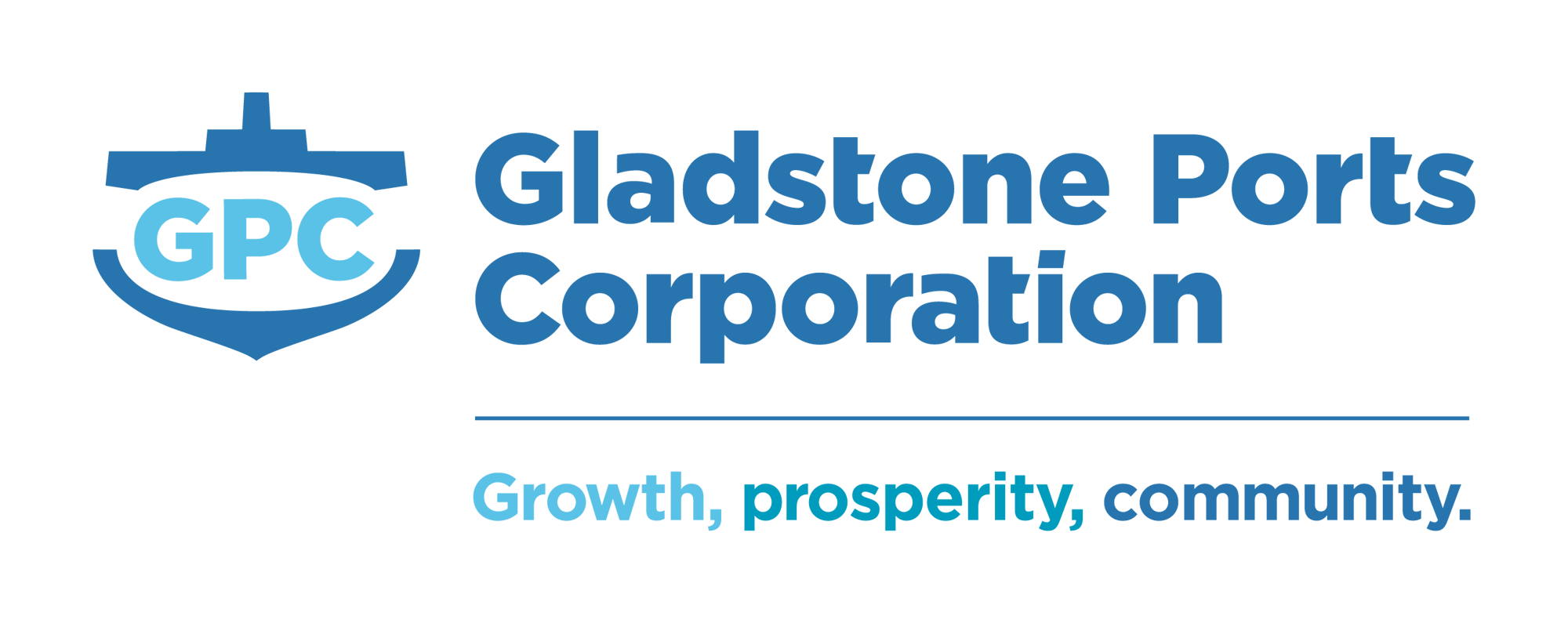
What our clients say
Geoff Irvine
Rockwell Automation
“We are delighted to have collaborated with MRA and this high value application.
The Smart Stockyard Management System is a key piece in bringing the “Connected Mine” to life for our mining customers.”
What our clients say
Anthony Manousso
Capcoal Control System Coordinator, Anglo American
“We had a challenging 22km rope overland conveyor that was performing poorly, unable to correctly control the speed and tension. MRA analysed the problem and in their offsite simulation environment came up with a revised control strategy and coal tracking system that was installed and commissioned in 2 days and has been running perfectly for 4 years. MRA has since reviewed all our rope conveyor control strategies and train load out systems.”
What our clients say
Travis Burton
Port Kembla
“The stockpile modelling and laser optimisation were major factors in our efficiency gains.”
Resolving Troublesome Conveyor Systems
The client engaged MRA to undertake a review of a troublesome conveyor system implemented by another provider.
Our goal was to deliver an engineered solution that resolves the client's problems.
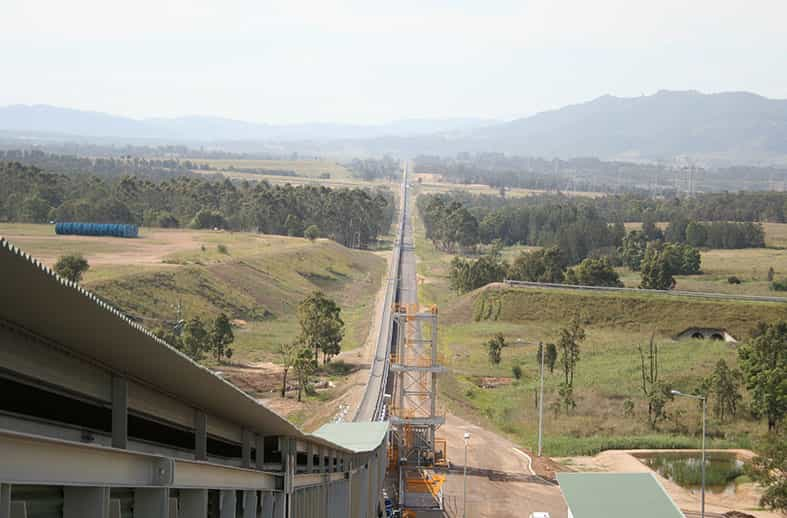